AI สำหรับใช้ในอุตสาหกรรม ผลิตภัณฑ์ ดูแลสุขภาพ
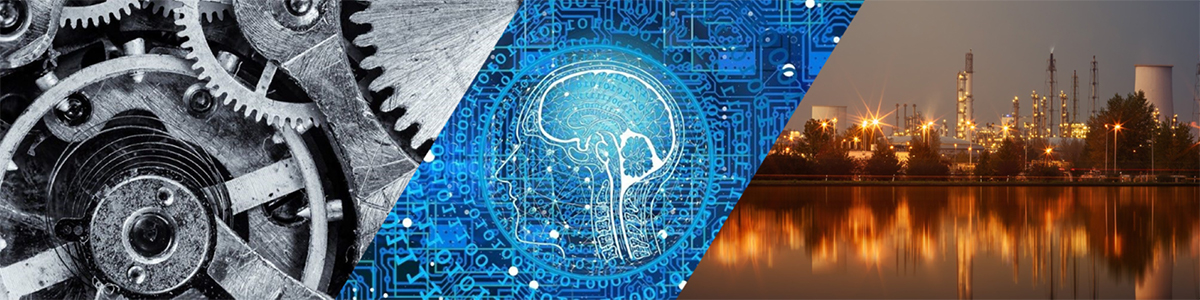
ปัญญาประดิษฐ์สำหรับการผลิต
System Invariant Analysis Technology
(SIAT, เทคโนโลยีการวิเคราะห์ค่าต่างๆระบบ) เพื่อค้นหาสิ่งที่ผิดปกติในระบบ
การนำไปประยุกต์ใช้
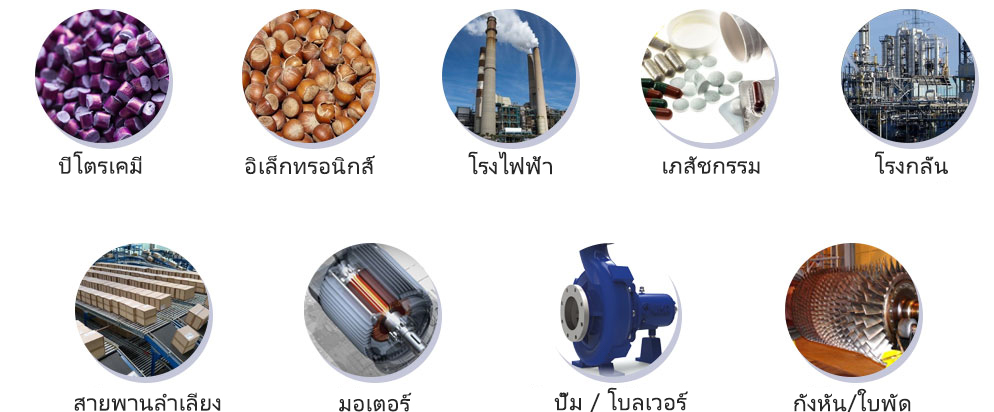
ความผิดปรกติ / การตรวจจับความผิดปรกติและการบำรุงรักษาเพื่อป้องกัน
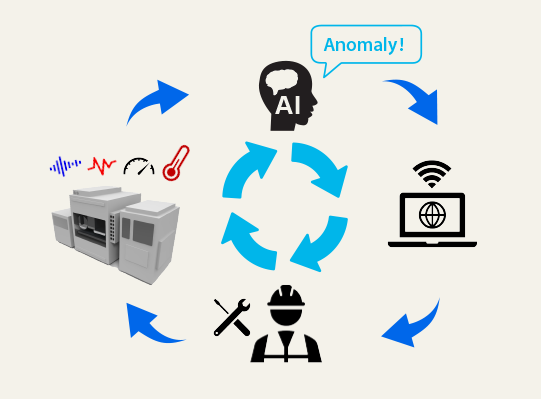
-
ตรวจจับอาการความผิดปรกติของระบบและเครื่องก่อนที่จะเกิดความเสียหายร้ายแรง
-
ช่วยลดรอบการบำรุงรักษาเครื่องจักรที่มากเกินคำจำเป็น
-
ช่วยลดต้นทุนการบำรุงรักษา
-
สามารถตรวจสอบเครื่องได้ตลอด 24 ชม.
-
การเตรียมการล่วงหน้าและการเปลี่ยนอะไหล่อย่างราบรื่น ลดเวลาหยุดทำงานของเครื่อง
-
การตรวจสอบกระยะไกล
-
สามารถวัดและตรวจสอบค่าพารามิเตอร์ได้อย่างง่ายดาย
การควบคุมคุณภาพผลิตภัณฑ์
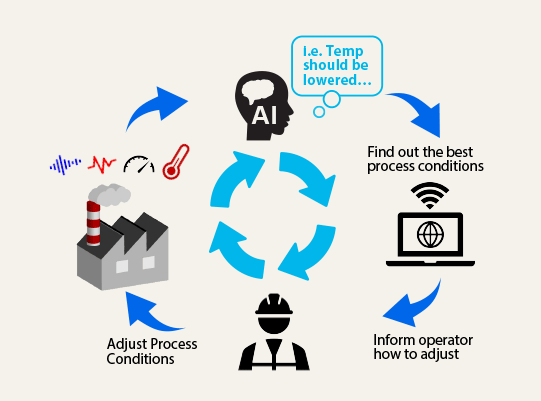
-
ตรวจพบความผิดปรกติของเงื่อนไขในกระบวนการที่ไม่สอดคล้องกับพารามิเตอร์
-
รักษาความเสถียรและคุณภาพที่ดีที่สุดของผลิตภัณฑ์ขั้นสุดท้าย
-
ลดหรือขจัดผลิตภัณฑ์ที่ไม่ผ่านมาตรฐาน (NG)
-
เพิ่มประสิทธิภาพและลดชั่วโมงในการทำงานของผู้ปฏิบัติงาน
-
ลดกระบวนการที่ต้องใช้การตัดสินใจของผู้ปฏิบัติงาน
การตรวจสอบด้วยสายตา
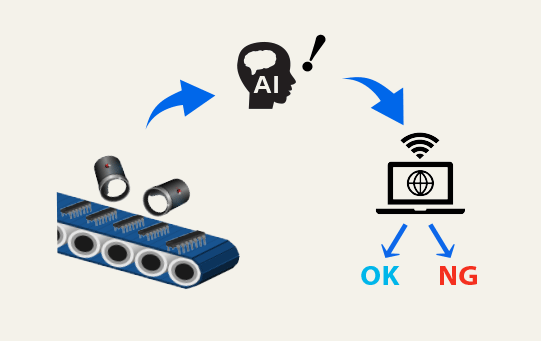
-
AI แยกความแตกต่างระหว่าง OK หรือ NG ได้ดีกว่าเกณฑ์การตัดสินแบบดั้งเดิม
-
ลดความผิดพลาดในการตัดสินของ OK หรือ NG ส่งผลให้ได้ผลตอบแทนสูงขึ้น
-
ลดแรงงานและค่าใช้จ่ายในการตรวจสอบคุณภาพ
-
เพิ่มอัตราการอัตราการประมวลผล (Throughput Rate)
ลดความผิดพลาดจากการตัดสินใจของผู้ปฏิบัติงาน
การทำงานของระบบนี้เป็นอย่างไร?
All copyright belongs to NEC Corporation
การตรวจจับความผิดปกติในระยะเริ่มต้น
ดึงความสัมพันธ์ที่ไม่เปลี่ยนแปลงจากข้อมูลอนุกรมเวลาซึ่งประกอบด้วยเซ็นเซอร์หลายตัว และสร้างแบบจำลองการตรวจสอบ
โดยอาศัยเทคโนโลยีการวิเคราะห์ค่าคงที่ในการตรวจจับความผิดปกติจากอนุกรมเวลาของเซ็นเซอร์ผ่านทางแบบจำลองที่สร้างขึ้น
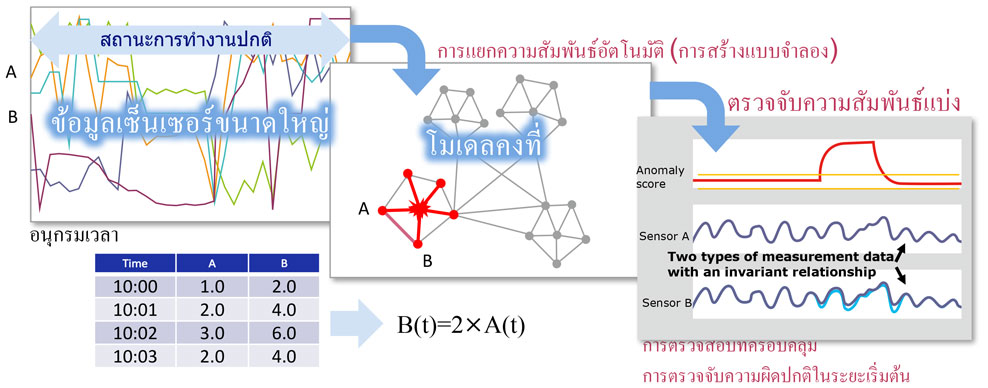
- 1. แต่ละความสัมพันธ์จะรวบรวมลักษณะเฉพาะขององค์ประกอบเป้าหมาย
- 2. โดยการค้นหาความสัมพันธ์จำนวนมาก ลักษณะความสัมพันธ์ของทั้งระบบสามารถพบได้จากการมองในมุมมองที่ต่างไปจากเดิม
- 3. สามารถเข้าใจสถานะการทำงานของระบบได้โดยการติดตามการเปลี่ยนแปลงของความสัมพันธ์ในแต่ละเหตุการณ์
กรณีศึกษา
กรณีที่ 1 – การสมัครโดเมนเพื่อใช้ในอวกาศของ Lockheed Martin
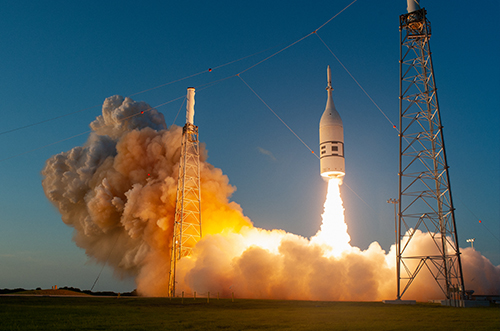
-
การทดสอบในการผลิตขั้นต้นและการศึกษาสถานการณ์ในการปฏิบัติงาน (ก่อนภารกิจจริงในอวกาศ)
-
ทำให้สามารถตรวจจับสิ่งผิดปกติเชิงรุกในระหว่างขั้นตอนการออกแบบ การพัฒนา การผลิต และการทดสอบ และสร้างสำเนาดิจิตอล (Digital Twin) ในระดับระบบ
-
สร้างแบบจำลองการทำงานปกติของรถยนต์จากเซ็นเซอร์ประมาณ 150,000 ตัว เพื่อสร้างความสัมพันธ์เชิงตรรกะกว่า 2,200 ล้านรูปแบบเพื่อใช้สำหรับการวิเคราะห์
Testimonial by Rockheed Martin. All copyright belongs to NEC Corporation
กรณีที่ 2 – ส่วนประกอบยานยนต์
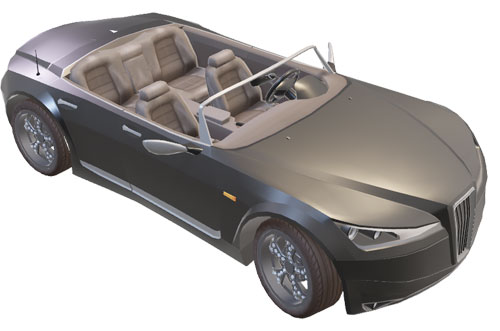
ความท้าทาย | ผลลัพท์ | |
---|---|---|
ไม่สามารถตรวจสอบคุณภาพของส่วนประกอบที่ถูกขึ้นรูป (Press Components) แบบเรียลไทม์ได้ | ![]() |
สามารถตรวจสอบได้แบบเรียลไทม์ |
ต้องมีการสำรองมากเกินไปเพื่อกรณีที่เกิดการเสียหาย | ![]() |
ช่วยตรวจจับความผิดปกติและลดจำนวนที่ต้องสำรอง |
ไม่สามารถหาสาเหตุที่แท้จริงได้ เนื่องจากเสียเวลาและพลังงานเพื่อหาสาเหตุที่ทำให้เกิดข้อบกพร่องเท่านั้น | ![]() |
การวิเคราะห์หาชิ้นงานที่บกพร่องด้วย AI ร่วมกับการวิเคราะห์สาเหตุโดยผู้ปฏิบัติงาน |
AI ถูกนำไปใช้กับกระบวนการผลิตชิ้นส่วนยานยนต์ เพิ่มเติมจากการปรับปรุงดังกล่าวข้างต้น
✓ ลูกค้าประสบความสำเร็จในการนำระบบ AI มาใช้กับองค์กรภายใน 5 วันแรก
✓ เพิ่มประสิทธิภาพระบบการซ่อมบำรุงและรอบการเปลี่ยนอะไหล่ เพื่อป้องกันงานซ่อมบำรุงทื่อการคาดการณ์
กรณีที่ 3 – เครื่องฉีดขึ้นรูป
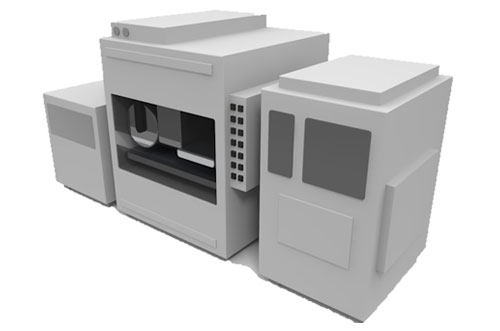
ความท้าทาย | ผลลัพท์ | |
---|---|---|
ระยะตรวจพบความบกพร่องล่าช้ากว่าระยะเวลาเมื่อเกิดความล้มเหลวมาก | ![]() |
ตรวจจับและพบความผิดปรกติตามเวลาจริง |
ผลิตภัณฑ์ที่บกพร่องถูกตรวจพบ แม้ว่าโดยลักษณะภายนอกจะไม่พบสิ่งผิดปรกติใดๆ | ![]() |
ตรวจจับข้อบกพร่องที่จะเกิดขึ้นได้อย่างรวดเร็ว ช่วยลดชิ้นงานที่มีความผิดพลาด |
ตรวจพบความขัดข้องของเครื่องจักร หลังจากพบผลิตภัณฑ์ NG | ![]() |
สามารถปรับสภาพและบำรุงรักษาก่อนผลิตผลิตภัณฑ์ NG ได้ |
ลูกค้าท่านนี้สามารถตรวจพบชิ้นส่วนที่ชำรุดภายหลังความผิดปกติของเครื่องจักรในการผลิต โดยเครื่องจักรยังคงผลิตสินค้าที่มีข้อบกพร่องอย่างต่อเนื่อง แม้ว่าเครื่องจักรทำงานผิดปกติอยู่ก็ตาม หลังจากแนะนำระบบ AI ลูกค้าสามารถพบความผิดปกติของเครื่องฉีดได้เร็วกว่าเมื่อก่อน ส่งผลให้ได้ผลผลิตสูงขึ้นและผลิตภัณฑ์ NG น้อยลง
กรณีที่ 4 – โรงกลั่น
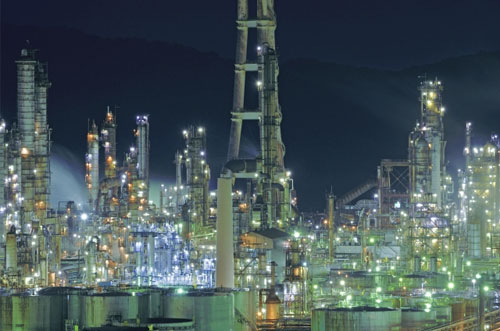
ความท้าทาย | ผลลัพท์ | |
---|---|---|
เพื่อให้ระบบตรวจจับข้อผิดพลาด กลายเป็นส่วนหนึ่งของเทคโนโลยีขั้นสูงทั่วไปที่ใช้โรงกลั่น | ![]() |
พบความสัมพันธ์ที่สำคัญระหว่างเซ็นเซอร์กว่า 500 ตัว (อุณหภูมิ ความดัน การไหล ตำแหน่งวาล์ว และระดับน้ำในหม้อไอน้ำ) |
ใช้เวลาและทีมงานจำนวนมากในการวิเคราะห์สาเหตุที่แท้จริง แต่ไม่สามารถตั้งค่าแผนการบำรุงรักษาระบบที่มีประสิทธิภาพได้ | ![]() |
สามารถแจ้งเตือนสถานะผิดปกติและตรวจพบข้อบ่งชี้ความล้มเหลวของอุปกรณ์ก่อนที่จะเกิดขึ้น ลูกค้าสามารถค้นหาสาเหตุและจุดที่ทำให้เกิดปัญหาที่แท้จริง |
AI ช่วยให้ลูกค้าค้นหาตัวบ่งชี้ความผิดพลาดได้เร็วกว่าระบบเดิมถึง 1 สัปดาห์ โดยอาศัยการวิเคราะห์แนวโน้มและลดผลกระทบให้เหลือน้อยที่สุด
การติดตามผล
Sector | Customer | System Contents |
---|---|---|
โรงงานไฟฟ้า | JERA Co., Ltd. | การตรวจสอบสัญญาณความผิดพลาดของโรงไฟฟ้าพลังความร้อน การตรวจสอบประสิทธิภาพที่ลดลง และการแสดงภาพสถานะการดำเนินงาน และการรวมการดำเนินงาน (โรงไฟฟ้า 4 แห่ง) พลังไอน้ำถ่านหิน 5 units แ ละกังหันก๊าซร่วม (Combined Gas Turbines) 20 units |
โรงงานไฟฟ้า | Medco Power Indonesia | การตรวจสอบสัญญาณความผิดพลาดที่โรงงานผลิตพลังงานความร้อน (GTCC) และทำให้การบำรุงรักษามีประสิทธิภาพมากขึ้น |
พลังงาน | JXTG Energy (Mizushima Refinery) |
ลดภาระงานและเพิ่มประสิทธิภาพของแผนการบำรุงรักษาโดยการตรวจจับสัญญาณผิดปกติของระบบสาธารณูปโภคและการซ่อมบำรุได้ล่วงหน้า |
ปิโตรเคมีคัล | Sumitomo Bakelite Co., Ltd | การตรวจจับสัญญาณความผิดปกติและการควบคุมสภาวะกระบวนการโดยอัตโนมัติทำให้คุณภาพของผลิตภัณฑ์มีเสถียรภาพ |
เหล็ก | Nippon Steel Corporation | การตรวจสอบความผิดปกติของระบบและการตรวจสอบคุณภาพแบบเรียลไทม์ในกระบวนการผลิต |
สำรวจอวกาศ | Lockheed Martin | การลดต้นทุนการพัฒนาและการปรับปรุงความปลอดภัยสำหรับการพัฒนายานอวกาศ การปรับปรุงความปลอดภัยโดยกระบวนการตรวจสอบที่มีความซับซ้อน |
รถไฟ | JR East | รักษาเสถียรภาพของระบบการทำงานโดยการตรวจจับสัญญาณความผิดพลาดของรถไฟและปรับปรุงประสิทธิภาพในการบำรุงรักษา |
อื่นๆ | JAXA Aerospace Exploration Agency (joint research) | การตรวจสอบความผิดปกติของเครื่องยนต์ของจรวดที่นำกลับมาใช้ใหม่ได้ และการนำไปใช้ในระบบตรวจสอบอากาศยาน |
อื่นๆ | Tohoku Univ. (Joint research) | การปรับปรุงประสิทธิภาพการตรวจสอบโดยใช้การตรวจสอบแบบไม่ทำลาย (Non-destructive inspection) |
อื่นๆ | Tohoku Univ. (Joint research) |
รักษาความเสถียรของคุณภาพในกระบวนการผลิตวัสดุ |
